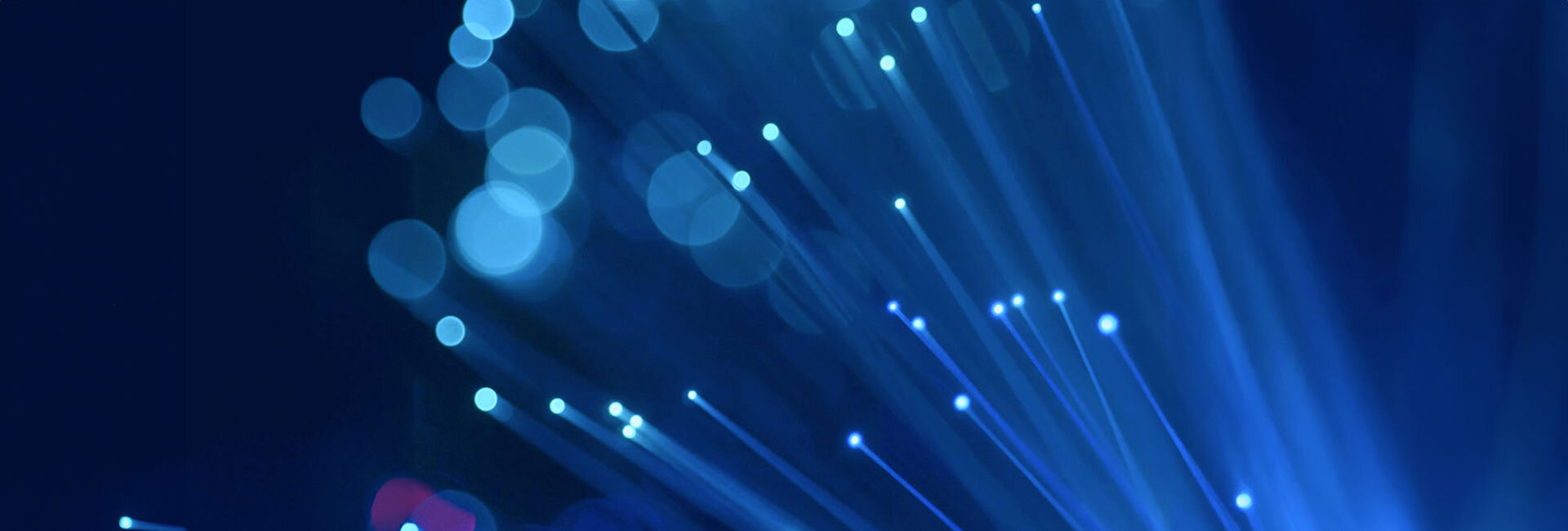
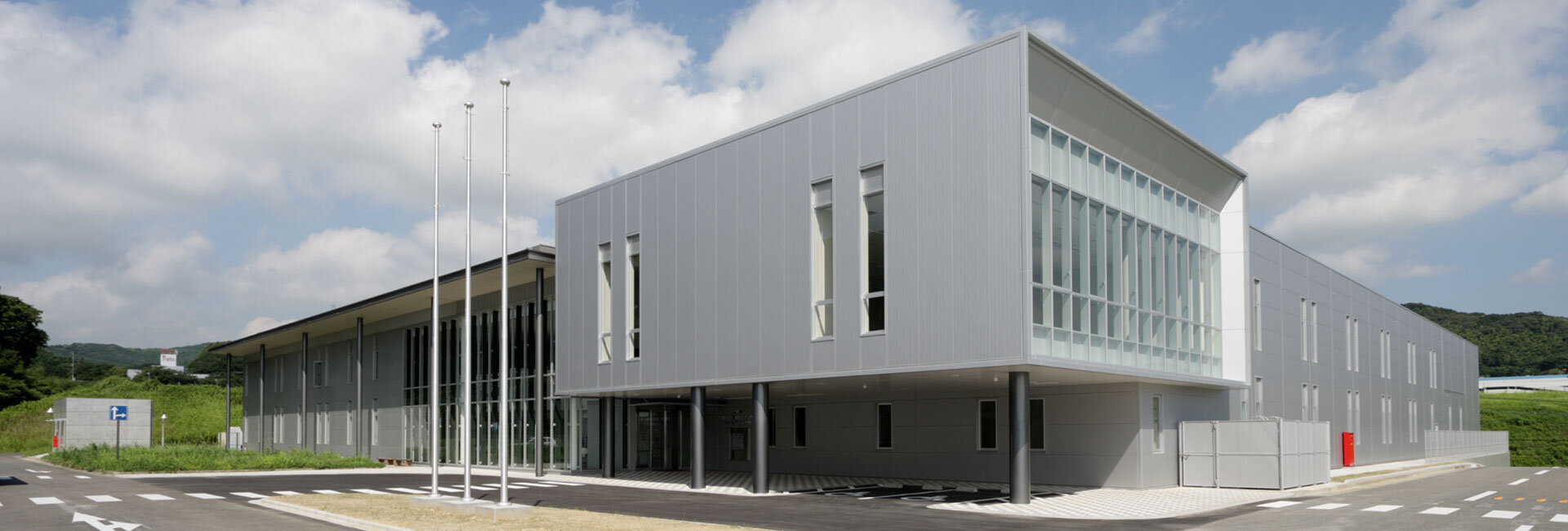
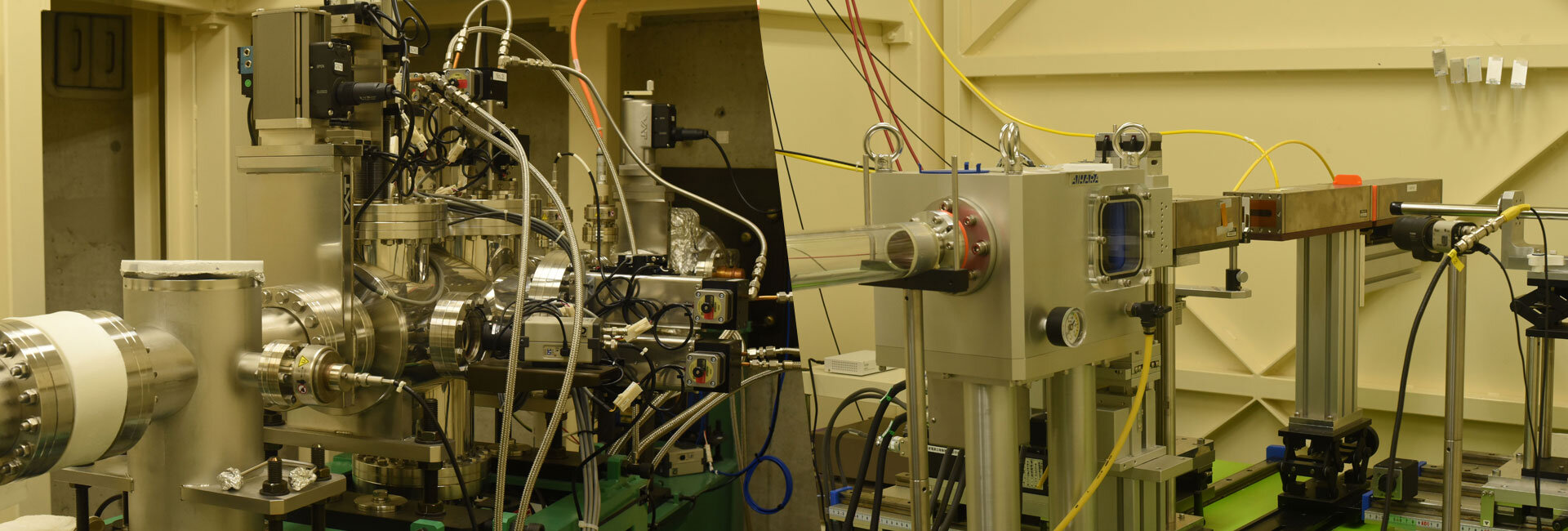
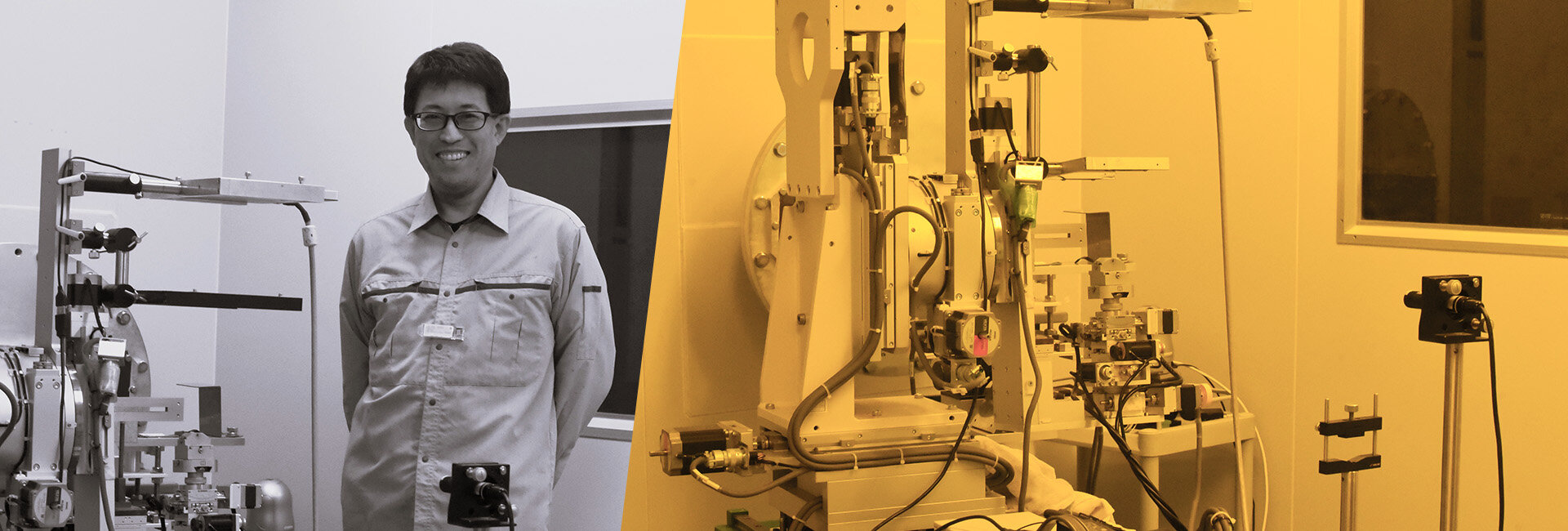
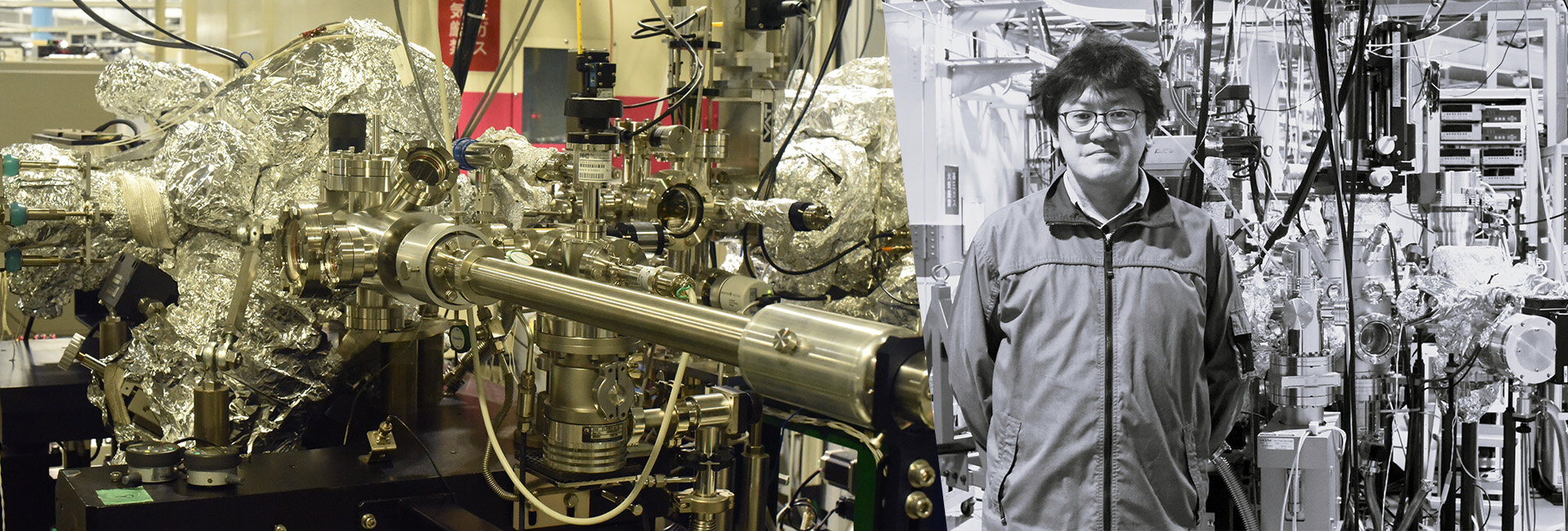
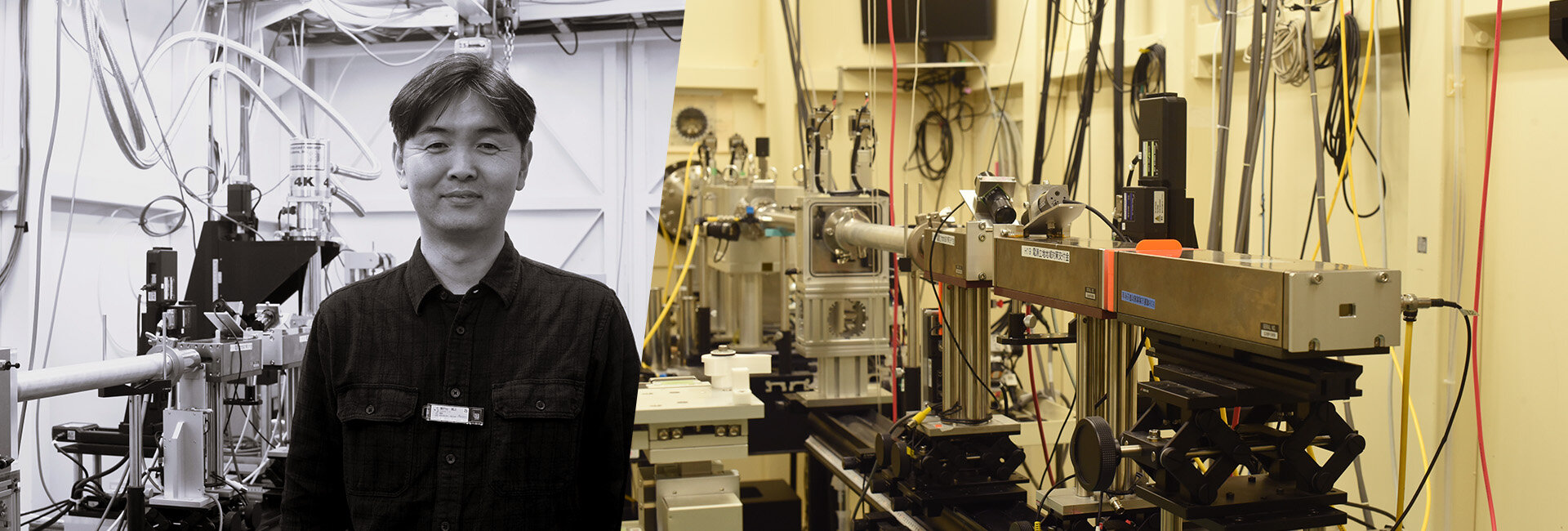
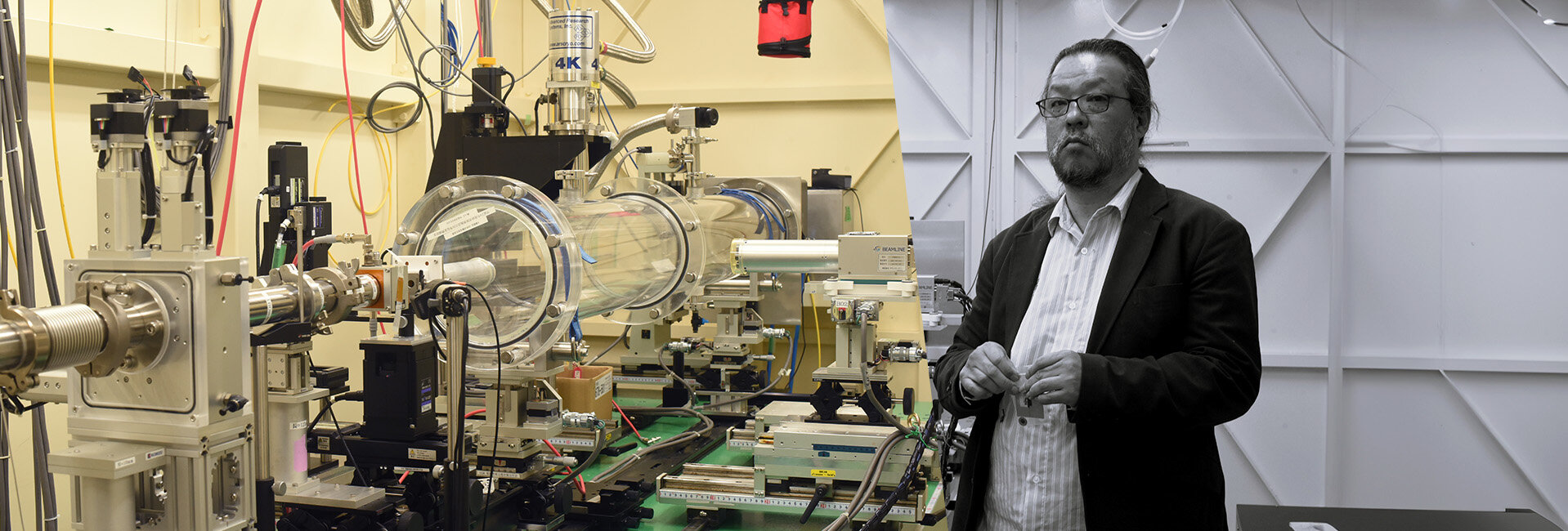
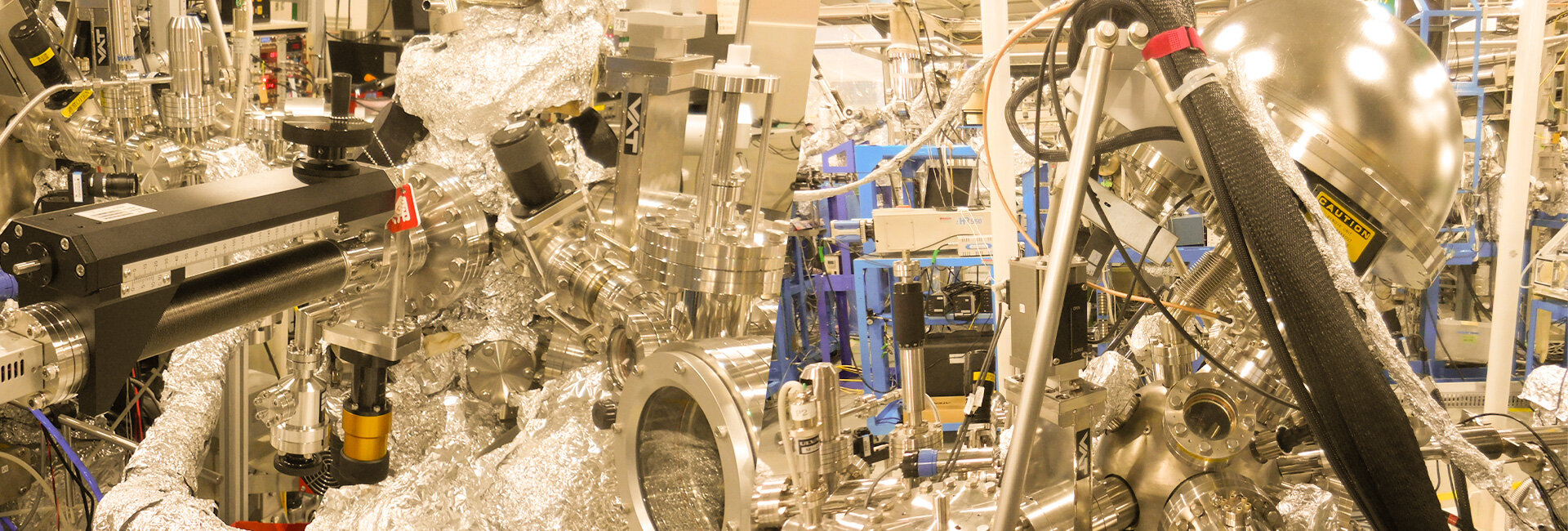
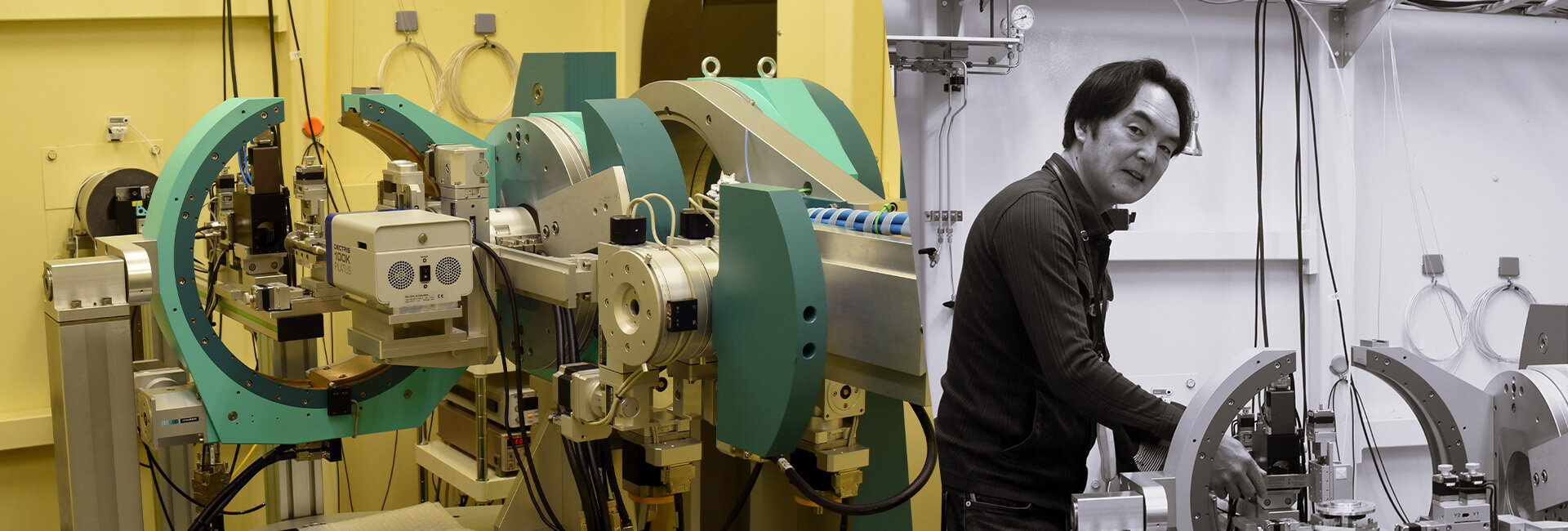
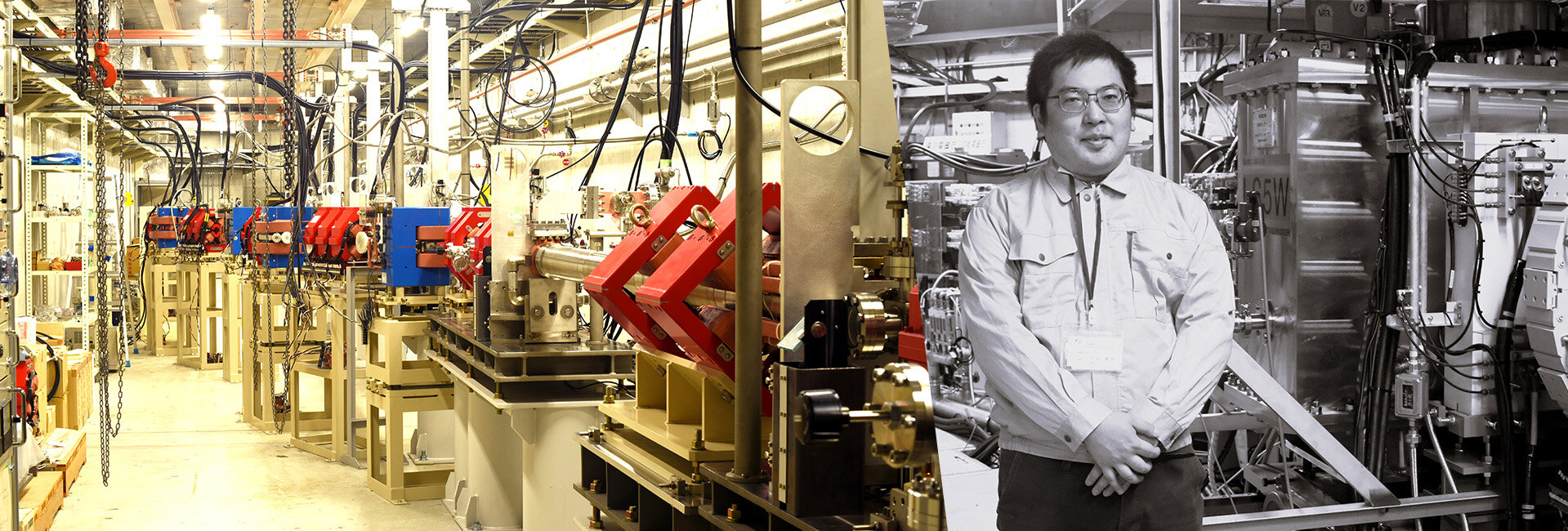
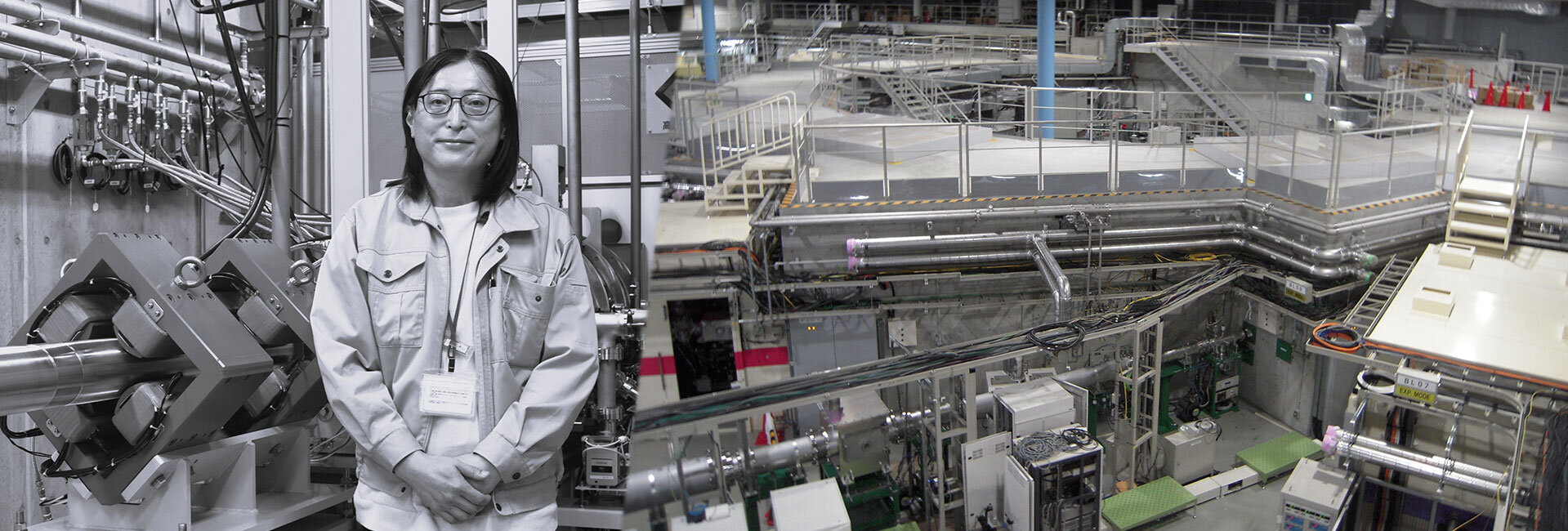
The Creation
of New Industries
of New Industries
シンクロトロン光で未来への扉を拓く
最先端科学が集うイノベーションの拠点
緊急のお知らせ
- 2025年度年間スケジュールカレンダーに、マシン停止期間における工事・作業情報を掲載しています [2025/02/28]
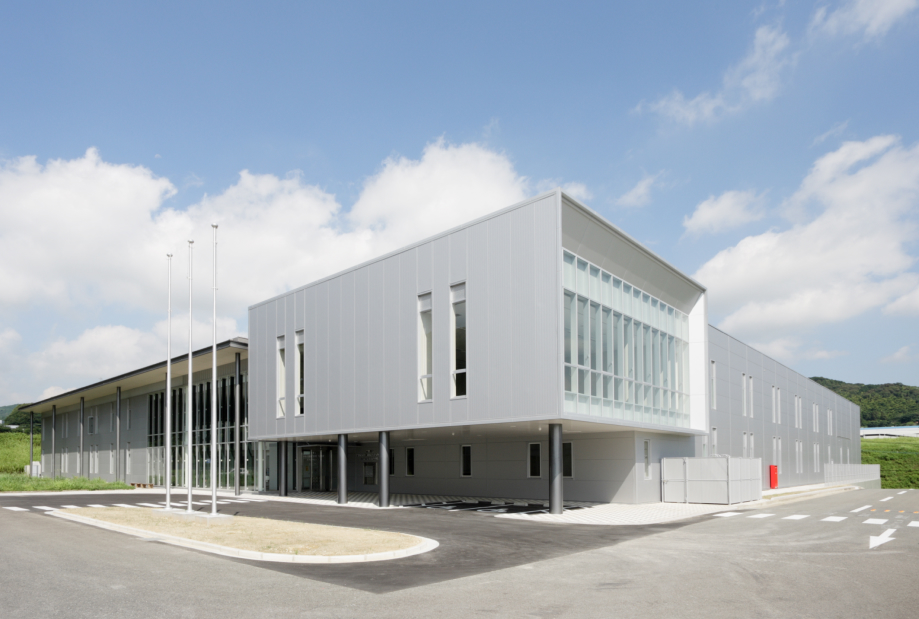
AboutSAGA-LSについて
九州シンクロトロン光研究センターは、「新産業創造、地域産業の高度化に向けたアジアワイドの高輝度光産業開発交流拠点」をコンセプトに設置された施設です。
Newsお知らせ
- すべて
- 課題募集
- 新着情報
- トピックス
- 研究成果
- 調達情報
- 採用情報
記事が見つかりません。